JB/T4040-2013重型板式给料机国家标准
重型板式板式给料机型式和基本参数
型式:沿板式给料机运行方向观察,传动方式分为右传动,左传动和双传动,按给料速度变化分为定速式和变频调速。
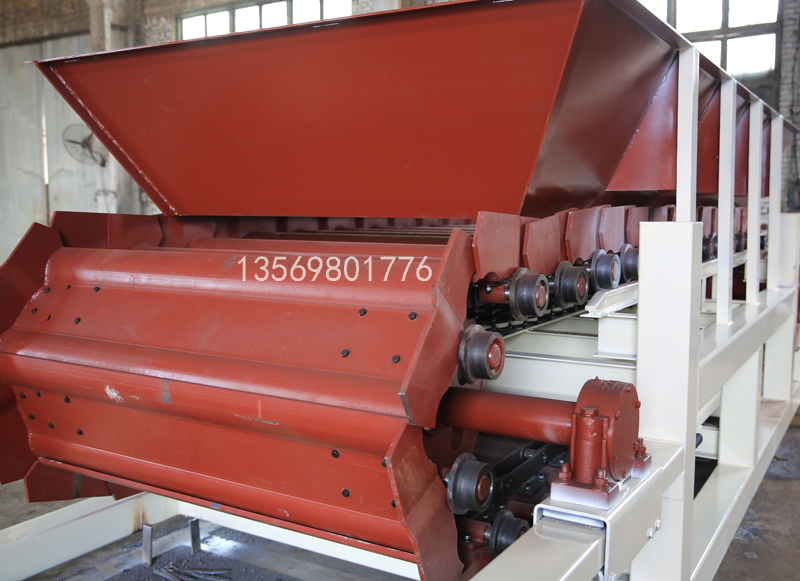
基本参数
板式给料机基本参数应符合以下规定
链板宽度B(mm) 中心距(M) 给料速度(m/s)
1000 4-20 0.02-0.20
1250 4-20 0.02-0.20
1600 6-18 0.02-0.20
1800 6-18 0.02-0.20
2000 6-18 0.02-0.20
2500 8-16 0.03-0.20
3150 8-12.5 0.03-0.20
3600 8-12.5 0.05-0.20
4000 8-12.5 0.05-0.20
注1:链板宽度为链板槽板之间有效宽度
注2:中心距指头尾轮之间沿机长投影的距离。
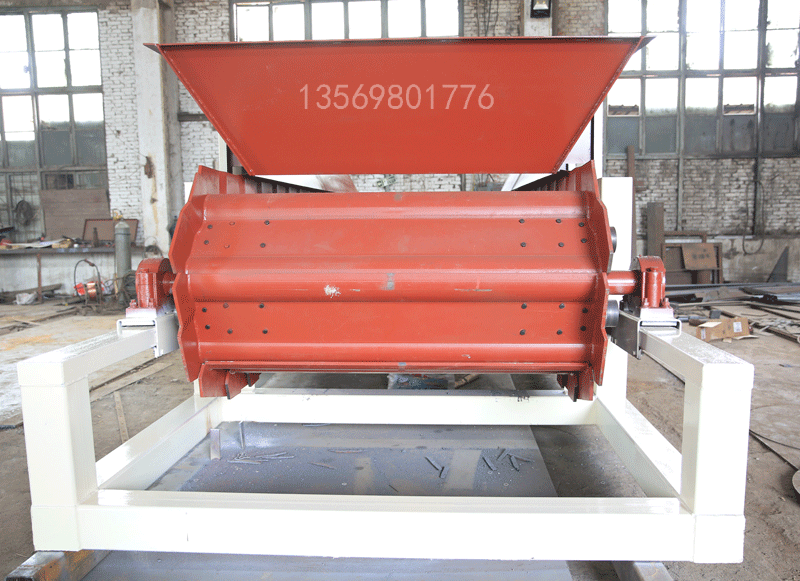
二:技术要求:
2.1重型板式给料机在下述条件下应该能可靠的工作
a)输送堆积密度小于2400Kg/m3的各种物料。
b)输送物料最大粒度不能大于0.8B。
c)料仓压力(单位为千牛KN)不应大于98B平方(链板宽度B,单位为米)
d)不卸空物料,不容许物料直接冲击链板,不在链板上爆破。
e)水平或向上倾斜输送,最大倾角不超过25°
f)工作环境为-20°--40°(稀油润滑装置除外)
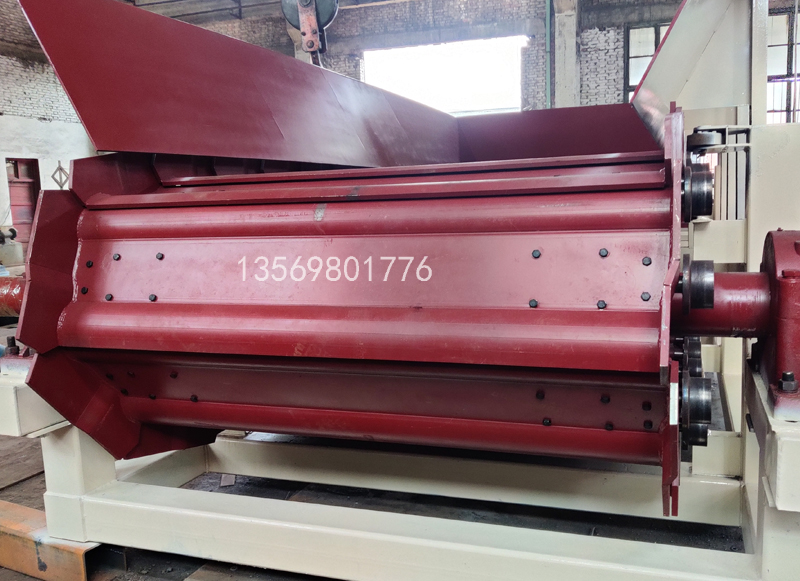
2.2链条选用破断拉力不应低于工作拉力的5倍。
2.3链板材质应选用力学性能不低于GB/T1591中的Q235或GB/T11352中的ZG270-500钢制造,链板焊接或铸造后应消除应力处理,链板搭接间隙应均匀,链板与链板之间搭接间隙不应大于5mm。
2.4尾部拉紧装置中的缓冲弹簧材质应选用力学性能不低于GB/T1222中的60Si2Mn钢制成,热处理后硬度为45HRC-50HRC,或采用复合弹簧,弹簧在规定负荷作用下,缓冲弹簧不应产生塑性变形和裂纹,复合弹簧不容许产生永久变形。
2.5选用的减速机应按相应标准和技术条件制造,直交减速器应符合GB/T8853的技术要求。
2.6链轮齿面不应有任何影响强度的缺陷,齿面硬度不应低于55HRC,淬硬层深度不应小于3mm。
2.7用于主轴装置和驱动装置中的涨套和锁紧盘,其安全系数不应低于2.
2.8机架二侧纵梁的直线度公差为1/1000,其全长的直线度公差应符合下表规定。
机架中心距m 3-5 5-10 10-15 15-20 20-25 25-30
直线度公差mm 4 5 6 8 10 12
2.9机架对角线之差不应大于下表规定
机架中心距m 3-5 5-10 10-15 15-20 20-25 25-30
对角线之差mm 4 5 6 8 10 12
2.10链轮轴线与水平面的平行度公差为链轮轴二轴承间距的0.15/1000
2.11链轮轴线对机架纵向中心线的垂直度公差为链轮二轴承间距的1/1000.
2.12拉紧轴轴线与水平面的平行度公差为拉紧轴二轴承间距的0.5/1000.
2.13拉紧轴轴线对链轮轴心线平行度公差为拉紧轴二轴承间距的1/1000.
2.14支重轮素线在机架横向与水平面的平行度公差为链板宽度的1/1000.
2.15托链轮素线在机架横向与水平面的平行度公差为链板宽度的1.5/1000.
2.16每侧链条宽度中线与链轮宽度中线的偏差不大于2mm。
2.17每侧链条宽度中线与支重轮宽度中线的偏差不大于2mm。
2.18链轮轴二端上的链轮装配后,其同名齿廓应在同一位置上。
2.19除锈等级应达到GB/T8923-1988中的Sa2.5级或St3级。
2.20装配后支重轮和托轮应转动灵活。
2.21在制造厂进行空负荷试车1小时,给料机运行平稳,无卡碰现象,链条与链轮运转正常。
2.22负荷试车在使用现场进行,其运行应平稳。
2.23轴承温升不应超过30°C,最高温度不应超过60°C。
2.24给料机噪声不应超过85db(A)。
2.25所有外露非加工与加工非配合金属件表面应涂底漆二层和面漆二层,涂漆应均匀,不能有脱漆,流痕,气泡等缺陷,其一般地区使用的漆膜总厚度为80um-100um,含有盐雾沿海地区使用的漆膜总厚度为200um-225um,涂漆前应将机件表面的残留物清除,保证漆膜光洁均匀,色泽一致.
2.26漆膜附着力应符合GB/T9286-1998中的2级规定。
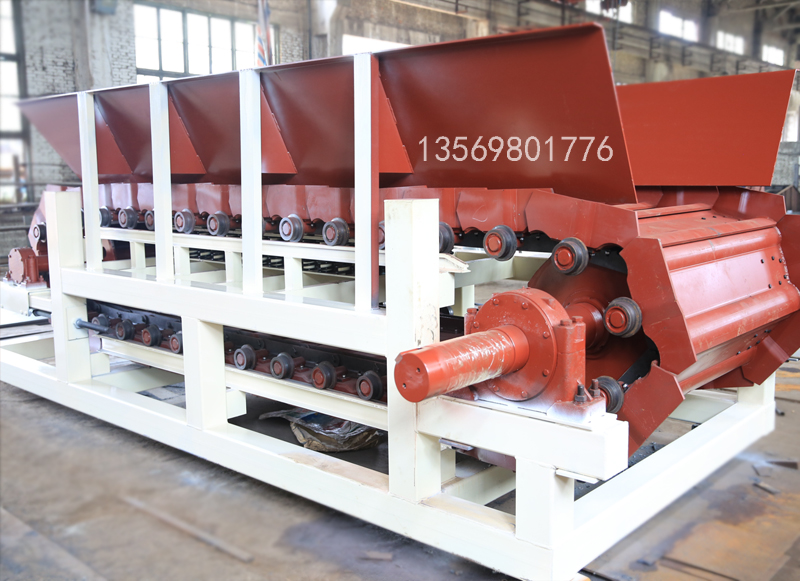
其余详见
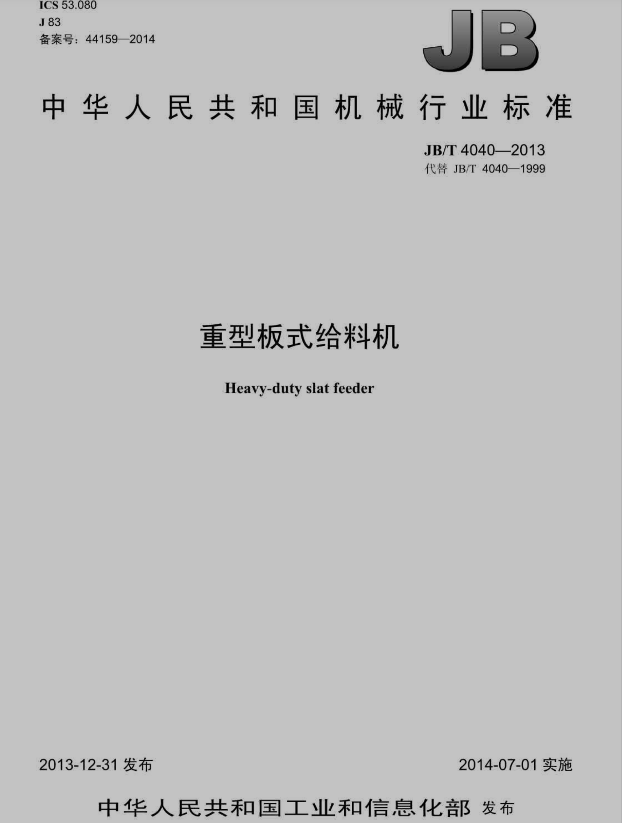
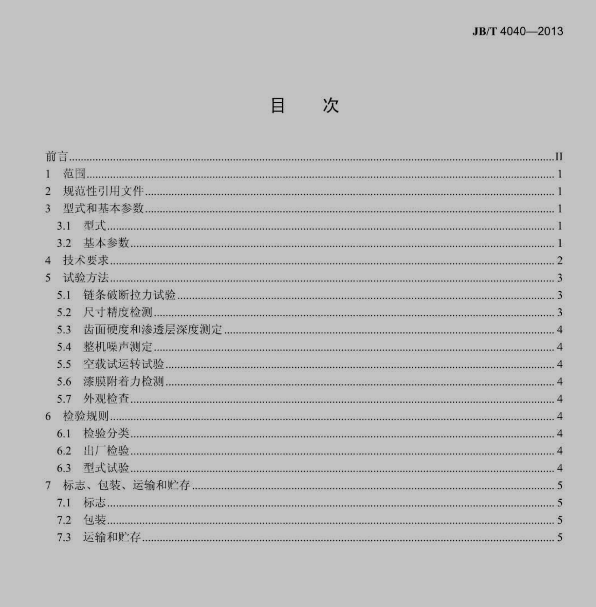
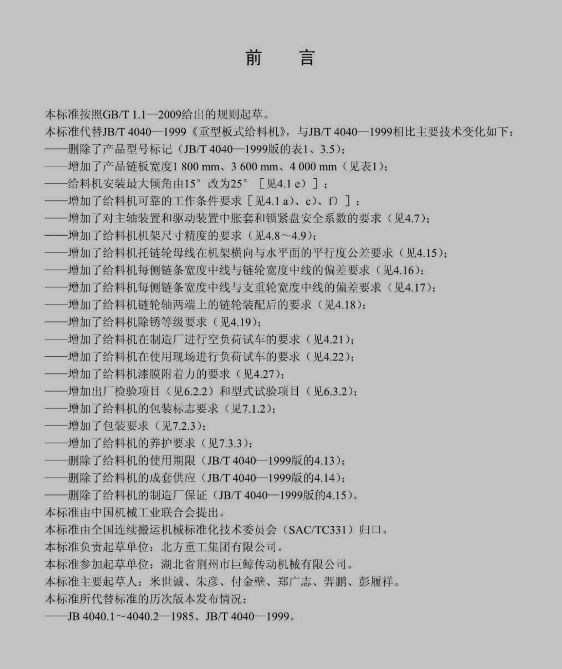
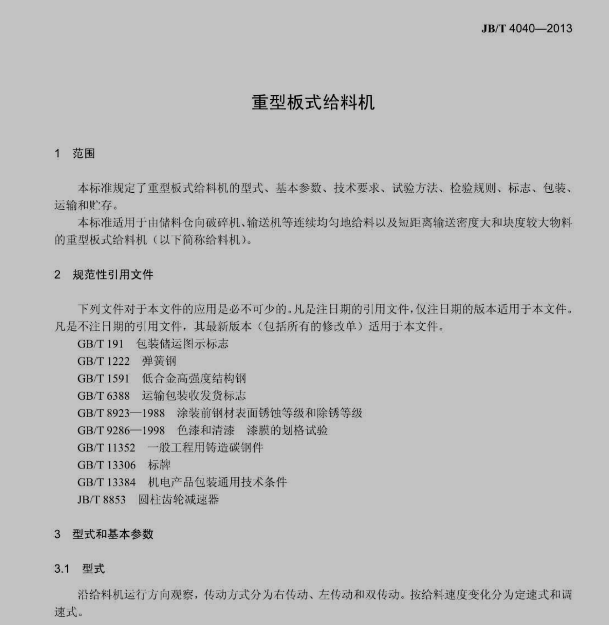
编辑:曹耀光